KZ Story
Korea Zinc shares the brand values and future vision of the company
[Metal Unboxing 02] Struggle towards high-purity metal extraction
2024-04-12
Series 02
METAL
UN-
BOXING
Struggle towards high-purity metal extraction
01

Do minerals play a significant role in our daily lives?
While living our busy lives, we encounter numerous spaces and interact with a variety of objects. In this regard, the existence of the ‘mineral’ plays a role in helping us to live more convenient and better lives. We can easily access it in places we may not have considered.
First, the copy paper that office workers commonly use contains ‘limestone’ powder. Paper made with limestone increases the whiteness of the product, thereby enhancing printing performance. Additionally, it reduces the usage of natural pulp, such as wood, leading to a reduction in carbon dioxide emissions. The rare metal “antimony” is primarily used as a flame retardant. It is found in various plastic products such as automobile lead-acid batteries with fire-retardant materials to prevent easy ignition, as well as in cable insulation materials and toys.
Even the padded jackets mostly worn on cold winter days contain minerals to increase the warming effect. One such mineral is ‘titanium’. Fabrics made with titanium capture body heat, providing extra warmth when worn. In addition, when mineral-rich ‘diatomite’ is used as a skincare face mask, it helps maintain healthy skin by absorbing impurities from the skin, calming and nourishing.
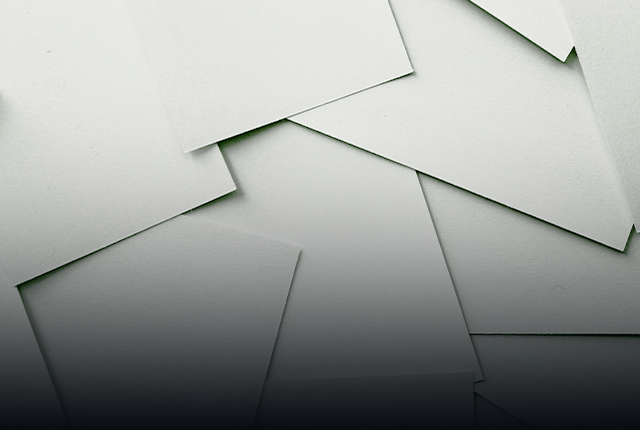
Copy Paper
improves printing
performance
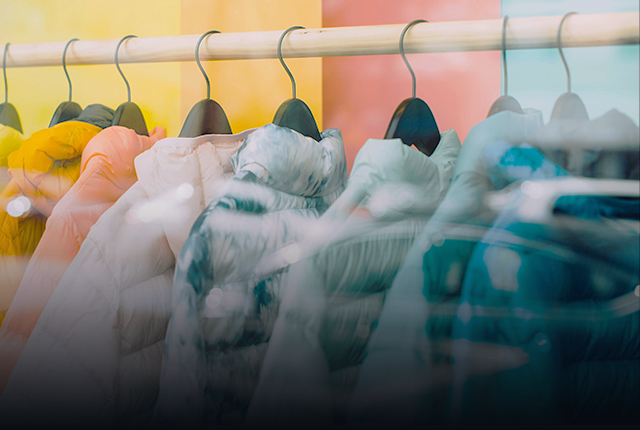
Winter
Padded Jacket
strong insulation and
anti-static properties
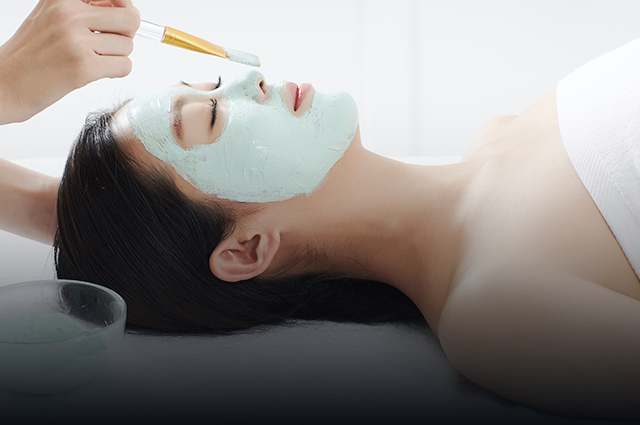
Skincare Face Mask
skin hydration and calming effects
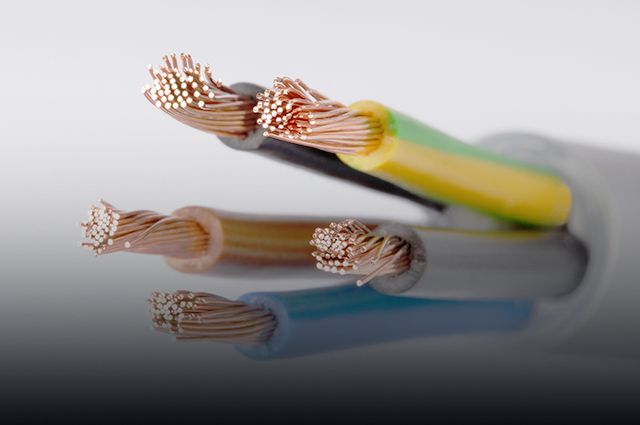
Cable Insulation
essential raw material for flame retardants

Limestone
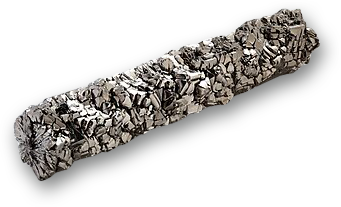
Titanium
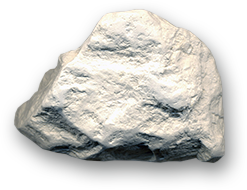
Diatomite
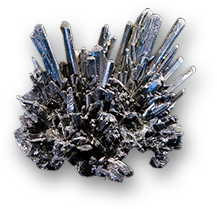
Antimony
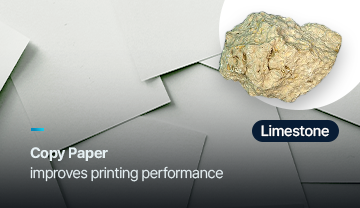
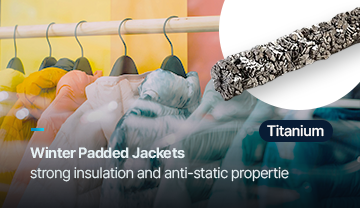
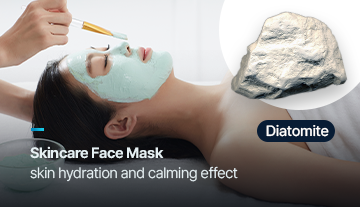
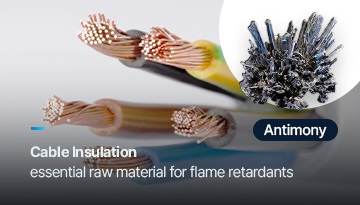
How many minerals are contained in modern life’s must-have item, the smartphone? There are over 20 types, including precious metals like gold and silver and various rare metals such as tantalum, gallium, and lithium. Referred to as urban mines, smartphones exploit a multitude of minerals in each component, spanning from the touch screen to the microphone, speaker, battery, and diverse sensors. As per Ministry of Environment statistics, the average discarded smartphone contains about 0.034g of gold. Recycling one ton of discarded smartphones, which can produce 300-400g of gold, underscores the considerable role smartphones play in mineral consumption, given that extracting a similar quantity of gold from natural ore typically requires processing several tons.
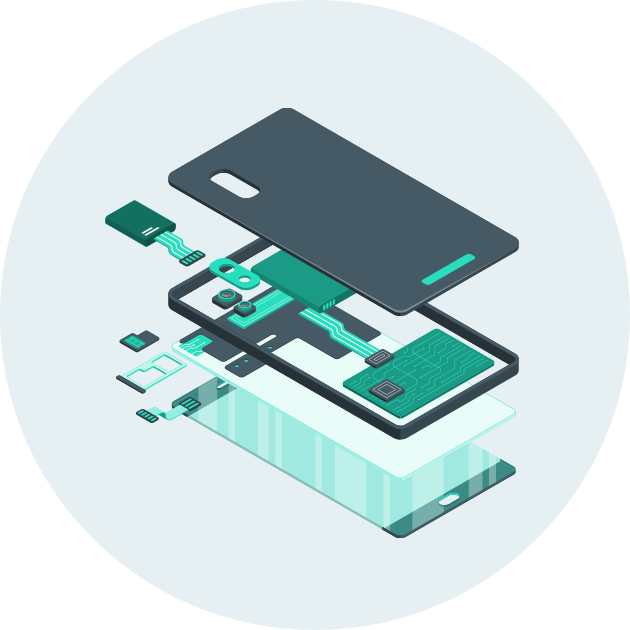
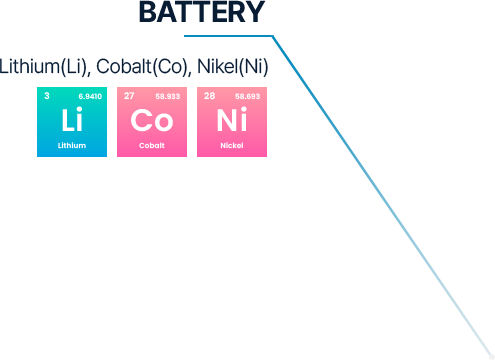
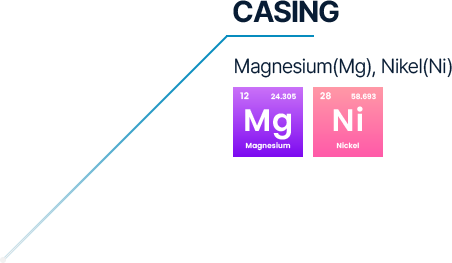
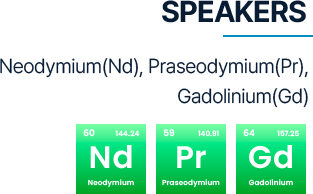
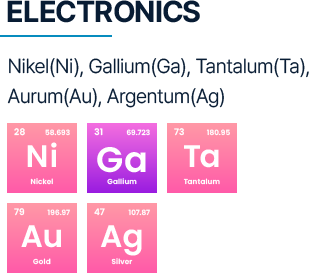
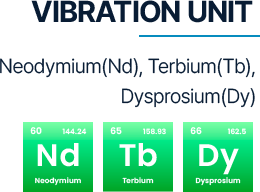
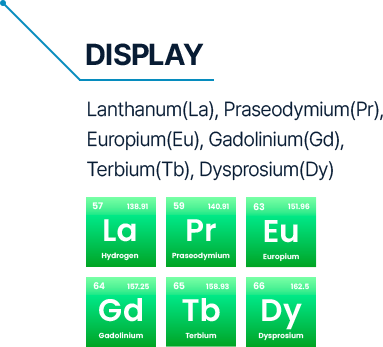
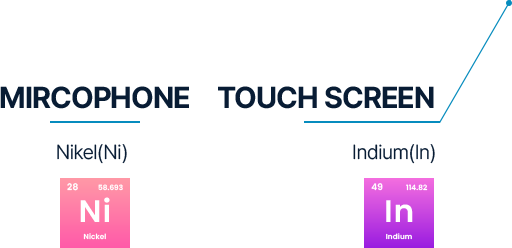
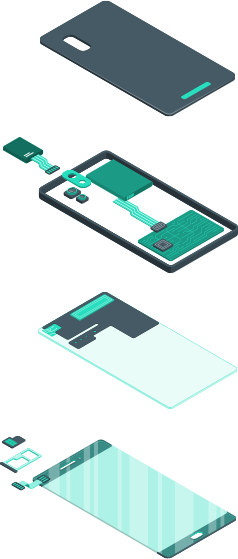
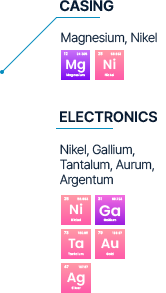
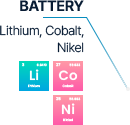
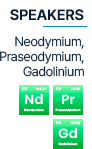
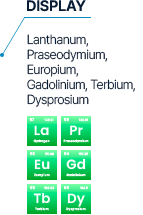
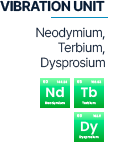
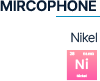
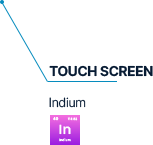
02

How are numerous metals and minerals obtained?
Minerals that are widely used in everyday life are hidden in the deep ground, so a mining process is needed to get these resources. The mining methods depend largely on the location of the desired minerals. The first method is open-pit mining. When minerals are located close to the surface, mining begins by gradually excavating them. Open-pit mining offers advantages such as higher productivity and lower risk of accidents compared to underground mining. However, if the excavated soil is not properly filled back in after mining operations cease, it can lead to environmental issues such as water pollution and flooding.
The second method is underground mining. When minerals are located relatively deep underground where open-pit mining is not feasible, tunnels are constructed underground to extract the ore. While underground mining may have lower competitiveness in terms of working conditions and productivity compared to open-pit mining due to factors like communication and safety for workers, it offers the advantage of being less affected by climatic conditions, allowing for year-round operation.
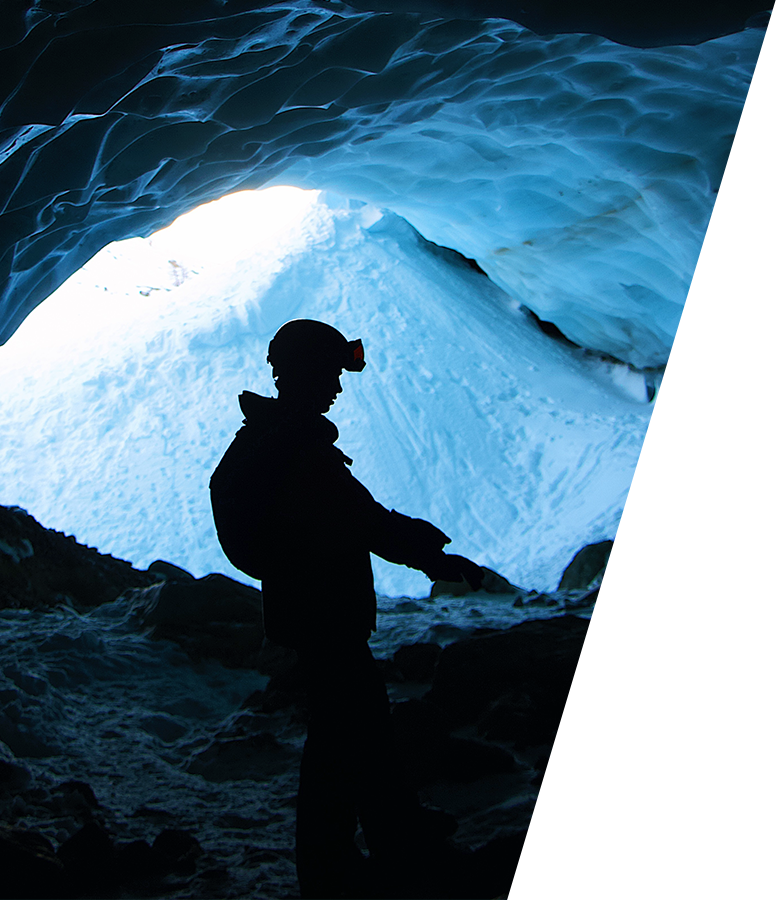
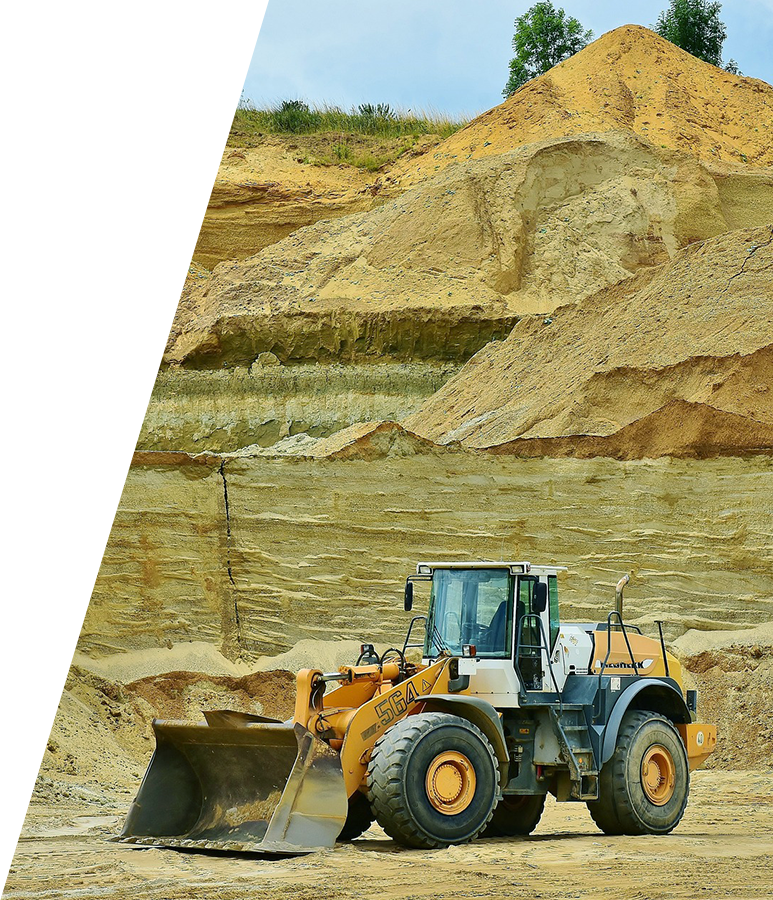
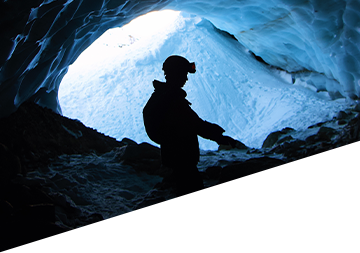
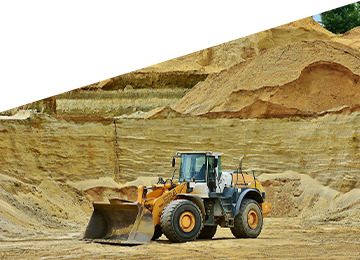
03

Does all mined ore need to be melted in a furnace?
It’s a well-known fact that iron ore, among the ores obtained through mining, is melted into red molten iron in high-temperature blast furnaces to produce steel. However, does the same process apply to non-ferrous metals, which collectively refer to metals excluding iron and its alloys?
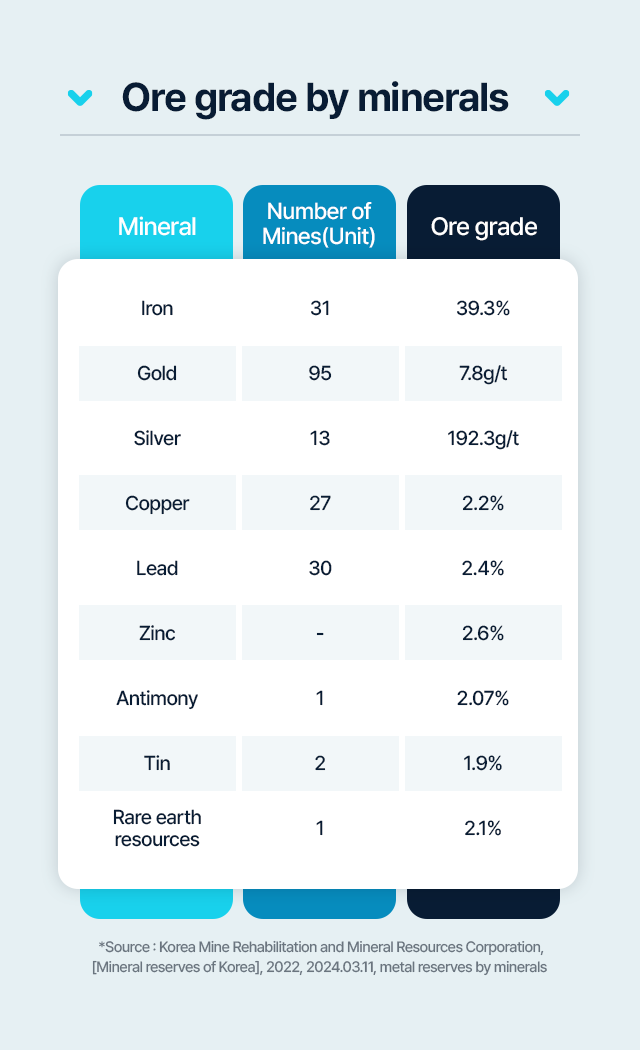
The iron content in iron ore is relatively high, whereas non-ferrous metals often contain impurities or gangue minerals mixed within the ore, resulting in significantly lower mineral content if directly put into the blast furnace.
In other words, due to the low grade* of the minerals, beneficiation and refining processes are required to extract the target metals and remove impurities, thus adding economic value.
*Ore Grade: A measure indicating how much useful substance is contained in the natural state of ore.
First of all, ‘beneficiation’, which is the process of selecting the ore needed, can be simply said to be a process of increasing the value of ore. In the mines, the ore is broken into small pieces, and then through the process of concentration, filtration, dewatering, and drying, ‘ore concentrate’ is produced in powder form with concentrated minerals.
The process of obtaining pure metal from the ore concentrate obtained through the beneficiation process using a chemical reduction reaction is called ‘smelting.’ The smelting process takes place in factories equipped with specialized facilities, not in the mines. In the case of zinc and lead products produced by Korea Zinc, it can be observed that the target metal grades within the ore concentrate are relatively high, reaching levels of around 50% to 60% each. Finally, the initial products yielded from smelting are subjected to the ‘refining’ process to enhance the purity of the metals even further.
Among the metals produced through this process, copper, aluminum, zinc, lead, nickel, and tin are classified as the six major non-ferrous metals, as they are important materials in industries such as automobiles, electrical and electronics, and construction.
Until non-ferrous metals reach our daily lives

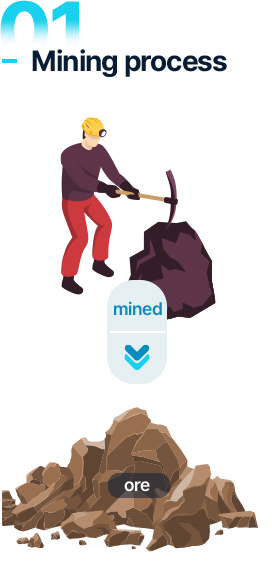
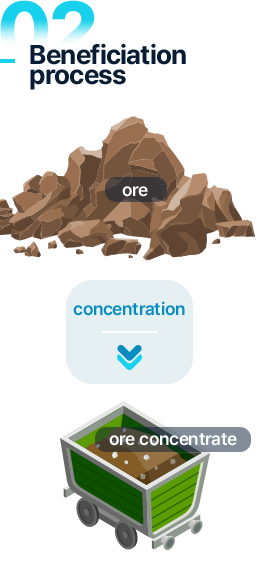
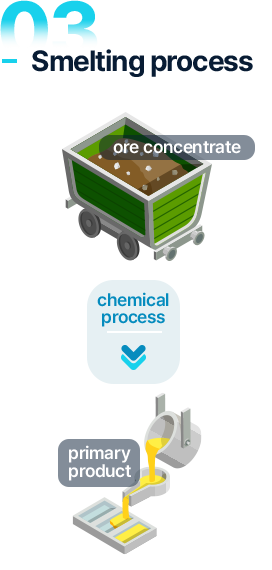
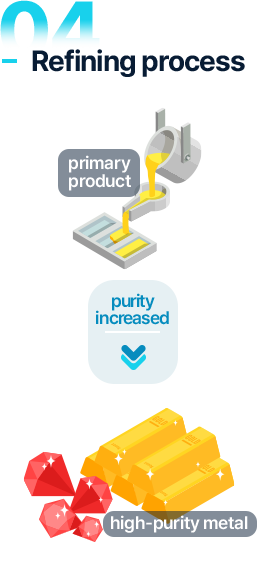
04

Do we have facilities in Korea producing high-purity metals?
Korea Zinc, established in 1974, has grown into the world’s leading smelting company based on Onsan refinery. Particularly, Korea Zinc’s electrolysis technology stands as one of the oldest and most used, with its zinc electrolysis plant boasting the largest production capacity globally among single refineries.
In the past, zinc production capacity, was only 50,000 tons, but now it has reached 1 million tons thanks to the electrolysis plant. Since the completion of the zinc plant in 1978, Korea Zinc has actively invested in process technology and quality research by establishing a research institute. As a result, the refinery with a capacity of 35,000 tons annually was completed in 1986 to produce both zinc and lead. Subsequently, Korea Zinc continuously expanded its production capacity through ongoing facility expansions.
Furthermore, Korea Zinc achieved commercial success with the world’s first implementation of the DRS lead smelting process in 2018. It not only produces energy-efficient and environmentally friendly lead but also introduces the TSL method to turn the remaining by-products into resources, thereby enhancing profitability.
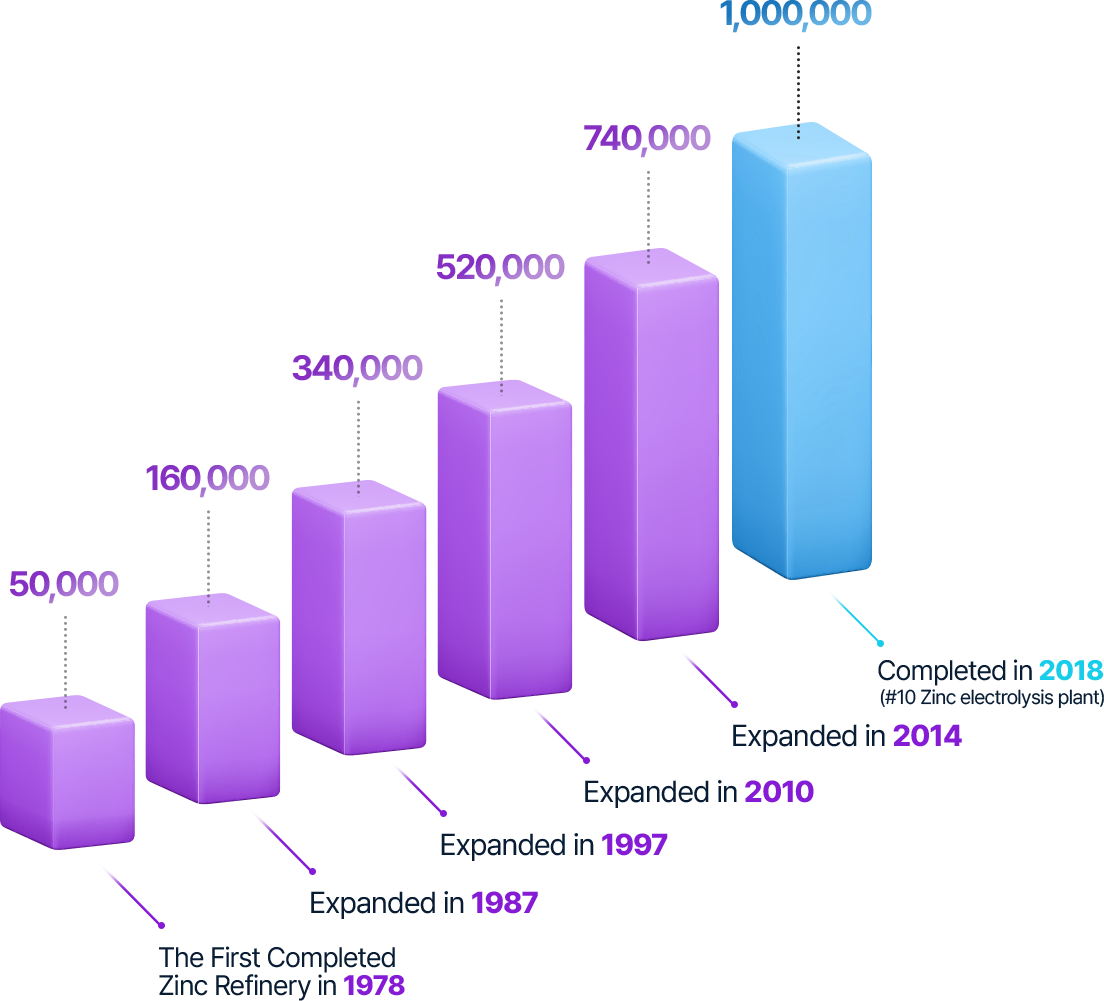
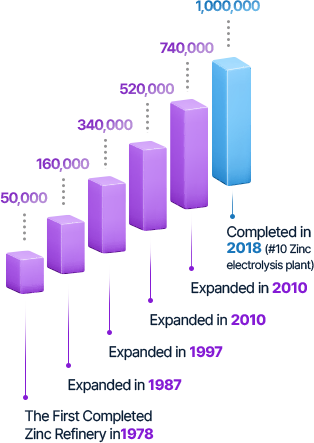
One of the reasons why Korea Zinc can lead the global non-ferrous metal industry is its annual production of over 1 million tons of more than 10 types of non-ferrous metals, such as zinc, lead, gold, silver, and copper. Zinc and lead each hold the top positions in the world market share, boasting the largest single refinery and the highest production capacity in the world. Moreover, Korea Zinc has firmly established itself as a global leader in the non-ferrous metal field with overseas sales accounting for 68%.
10 types of non-ferrous metals annually
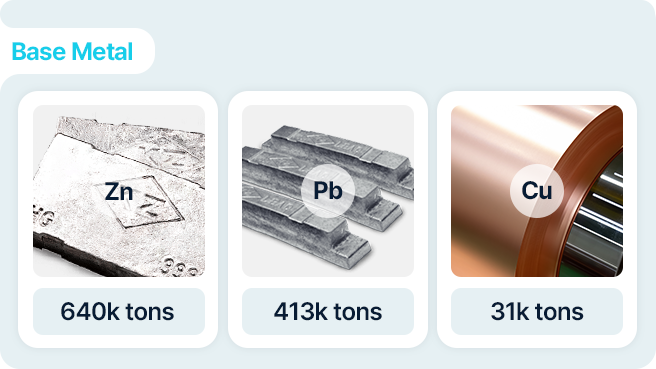
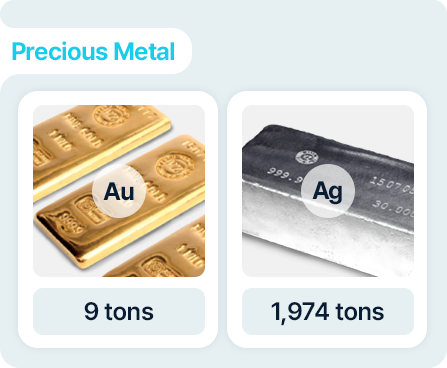
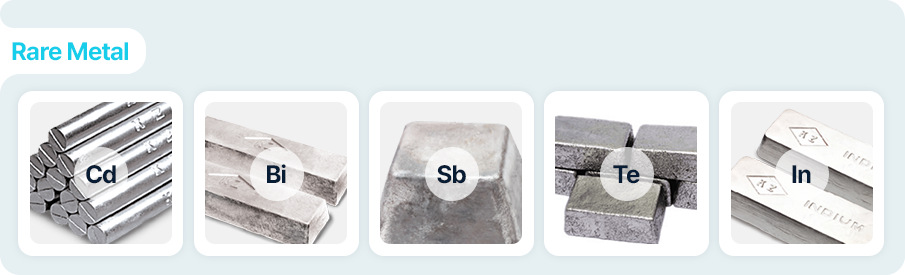
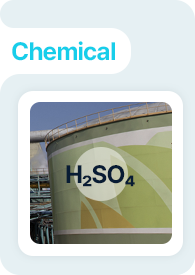
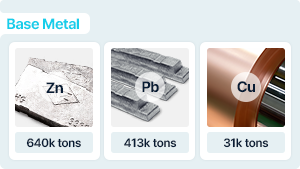
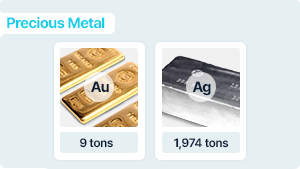
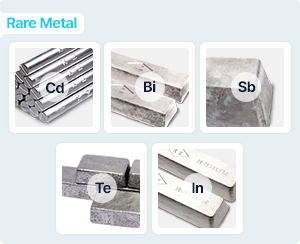
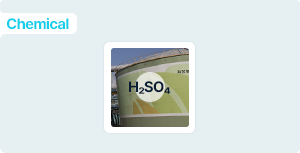
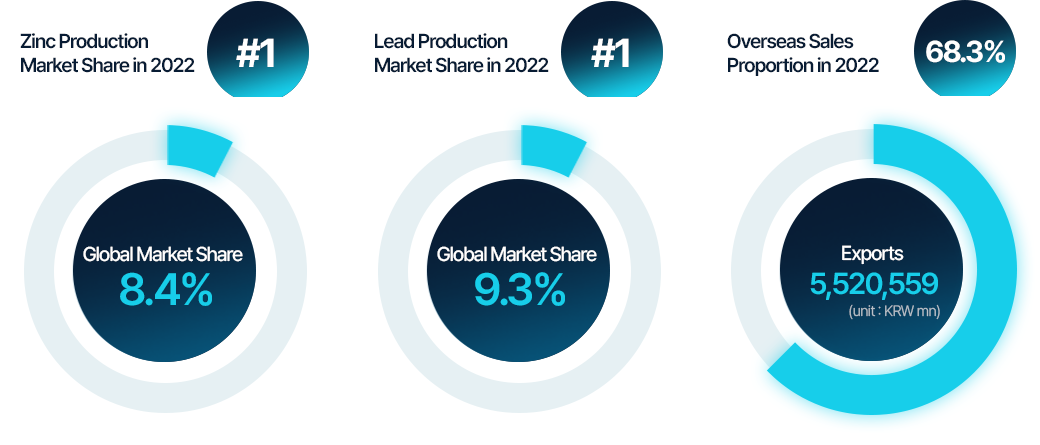
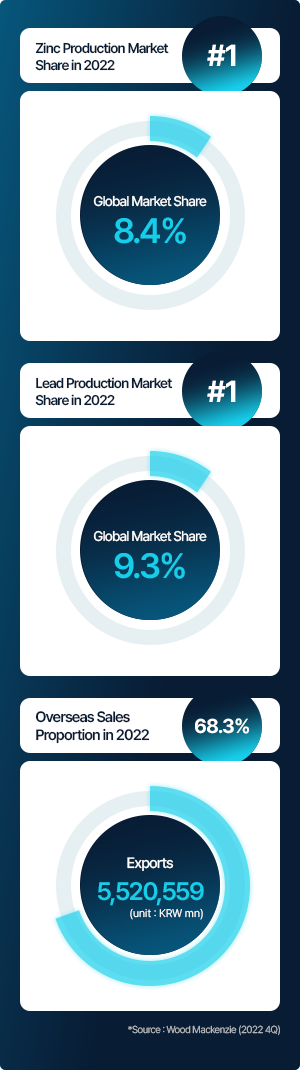
Furthermore, Korea Zinc plans to maximize sales of high-purity cathode copper and semiconductor sulfuric acid, which are considered a future growth driver in the smelting sector. Additionally, starting from the completion of the all-in-one nickel refinery in 2026, it plans to pursue an integrated process to maximize the recovery rate of the four major non-ferrous metals (zinc, lead, copper, and nickel).
In the future, Korea Zinc aims to lay the groundwork for sustainable expansion by tapping into new business opportunities such as rechargeable battery materials, resource recycling initiatives, and renewable energy. Leveraging the past 50 years of expertise in non-ferrous smelting technology, Korea Zinc seeks to establish itself in these emerging markets.

Korea Zinc,
Global No.1 Refining Company
Creating tomorrow’s value from today’s refining.
korea Zinc
METAL
UNBOXING